Smart solutions for a sustainable future
Our work
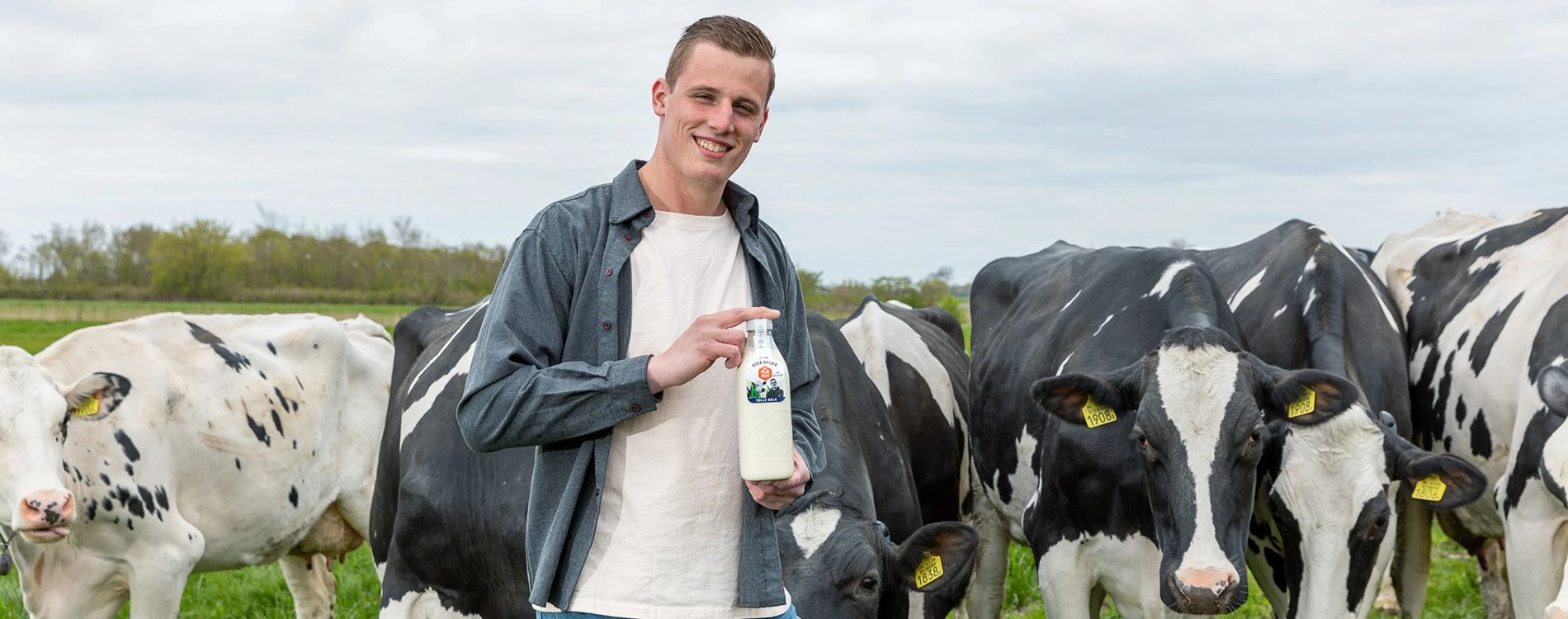
Mijn Melk
Lely
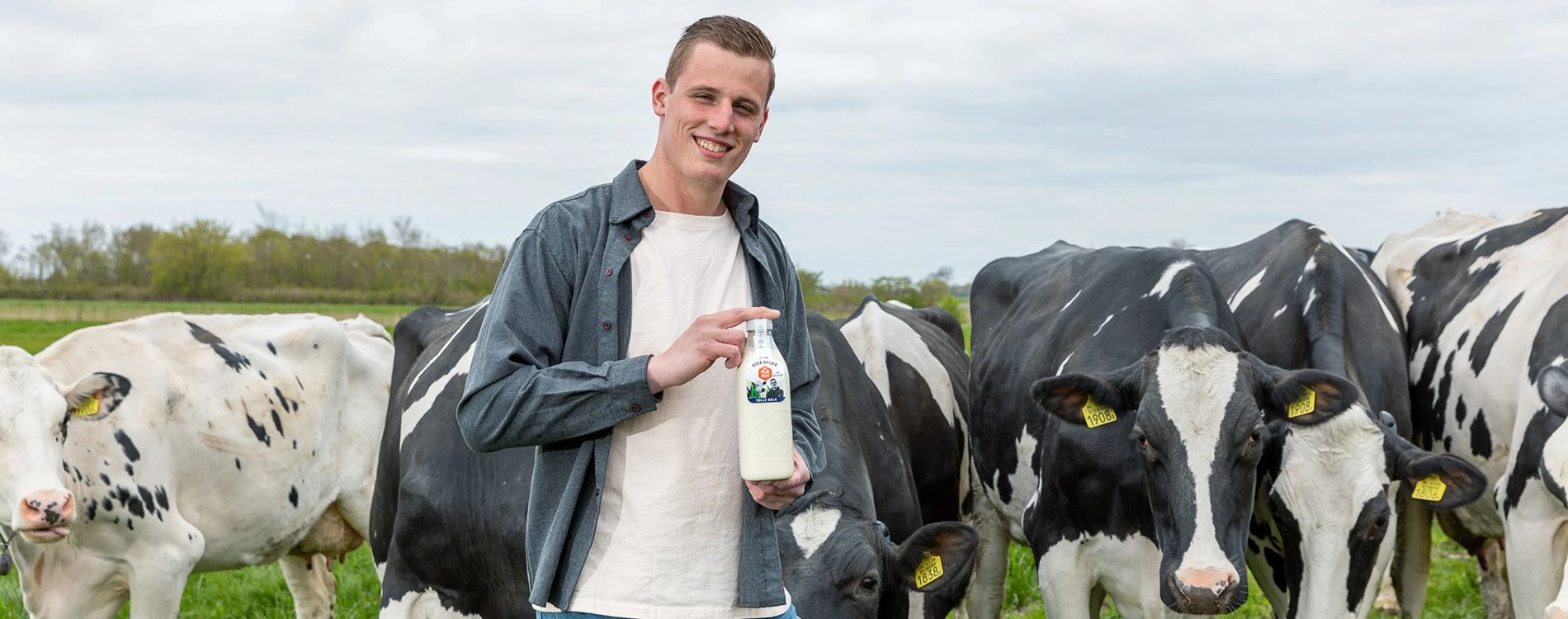
Mijn Melk
Lely
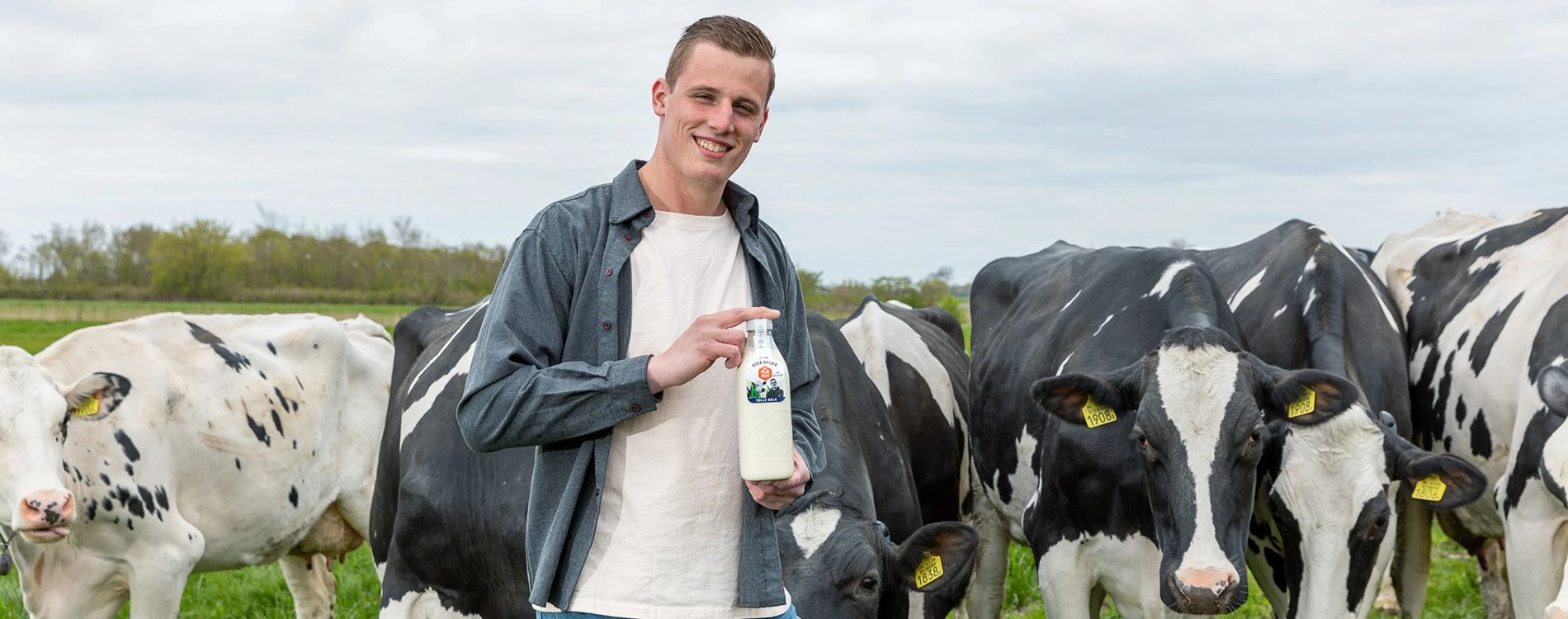
Mijn Melk
Lely
Empowering farmers to market local milk
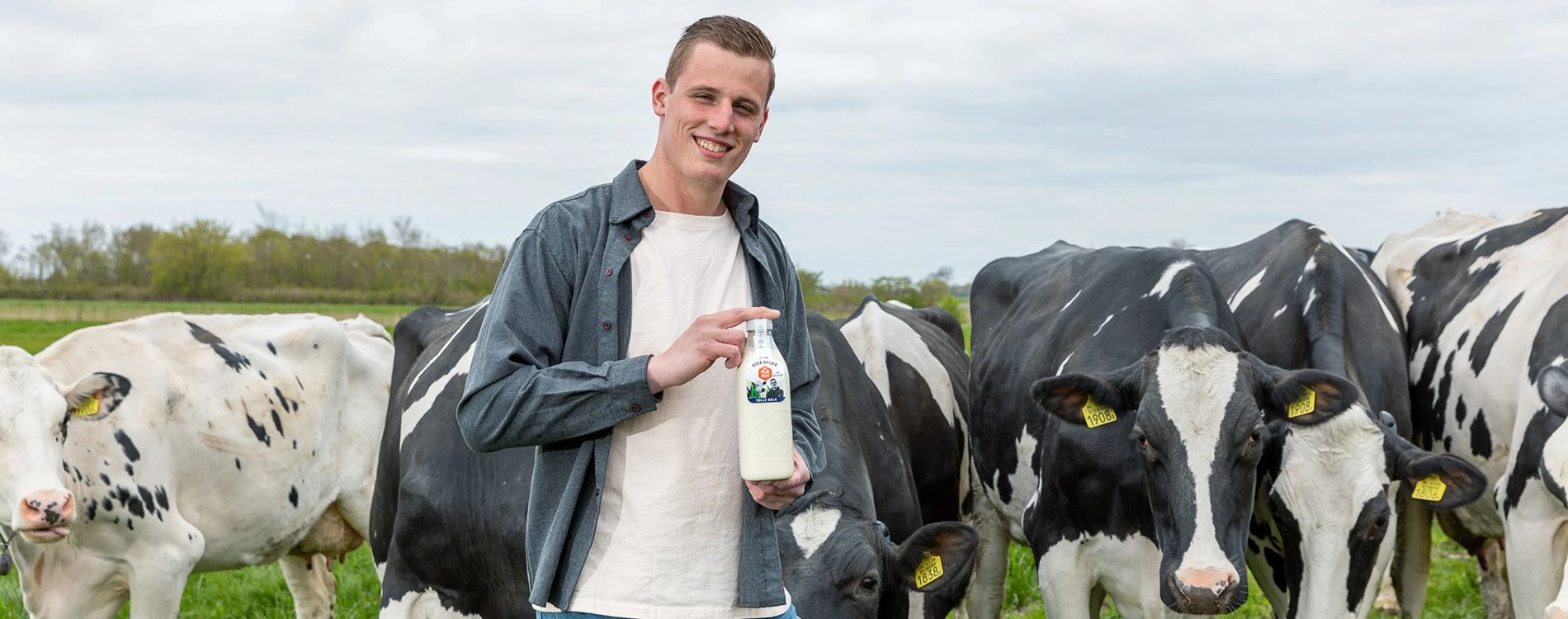
Mijn Melk
Lely
Empowering farmers to market local milk
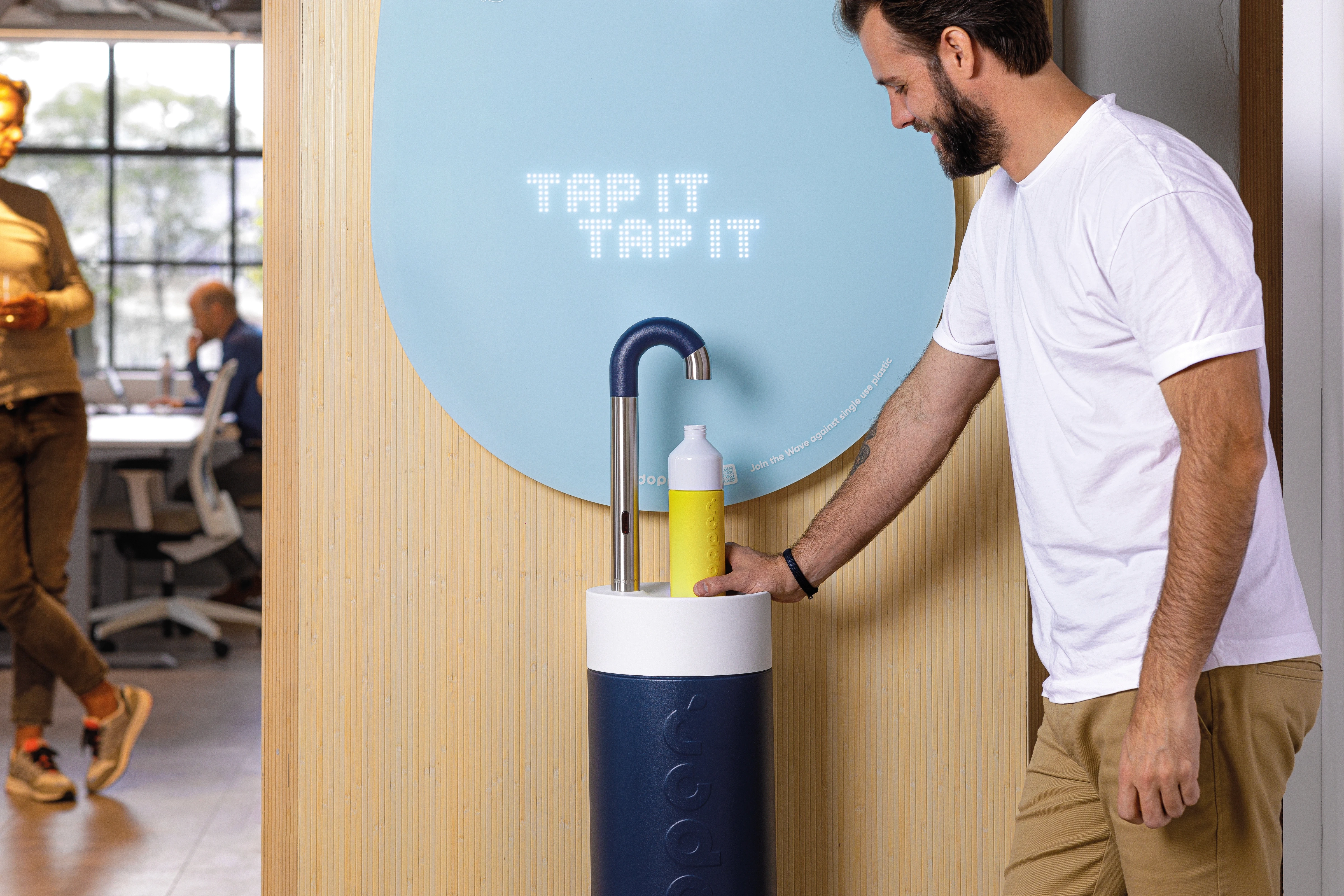
The Talking Tap
Dopper
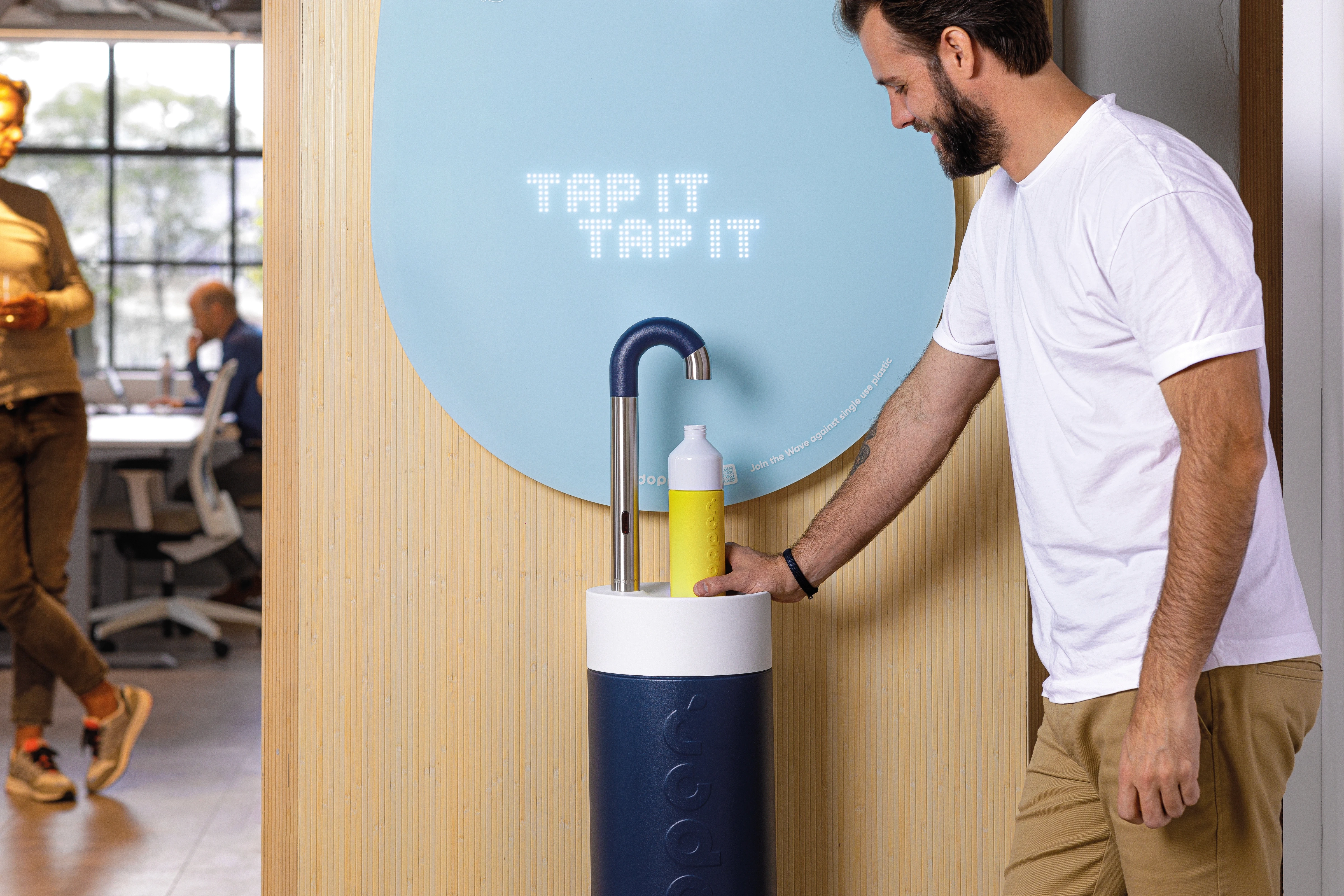
The Talking Tap
Dopper
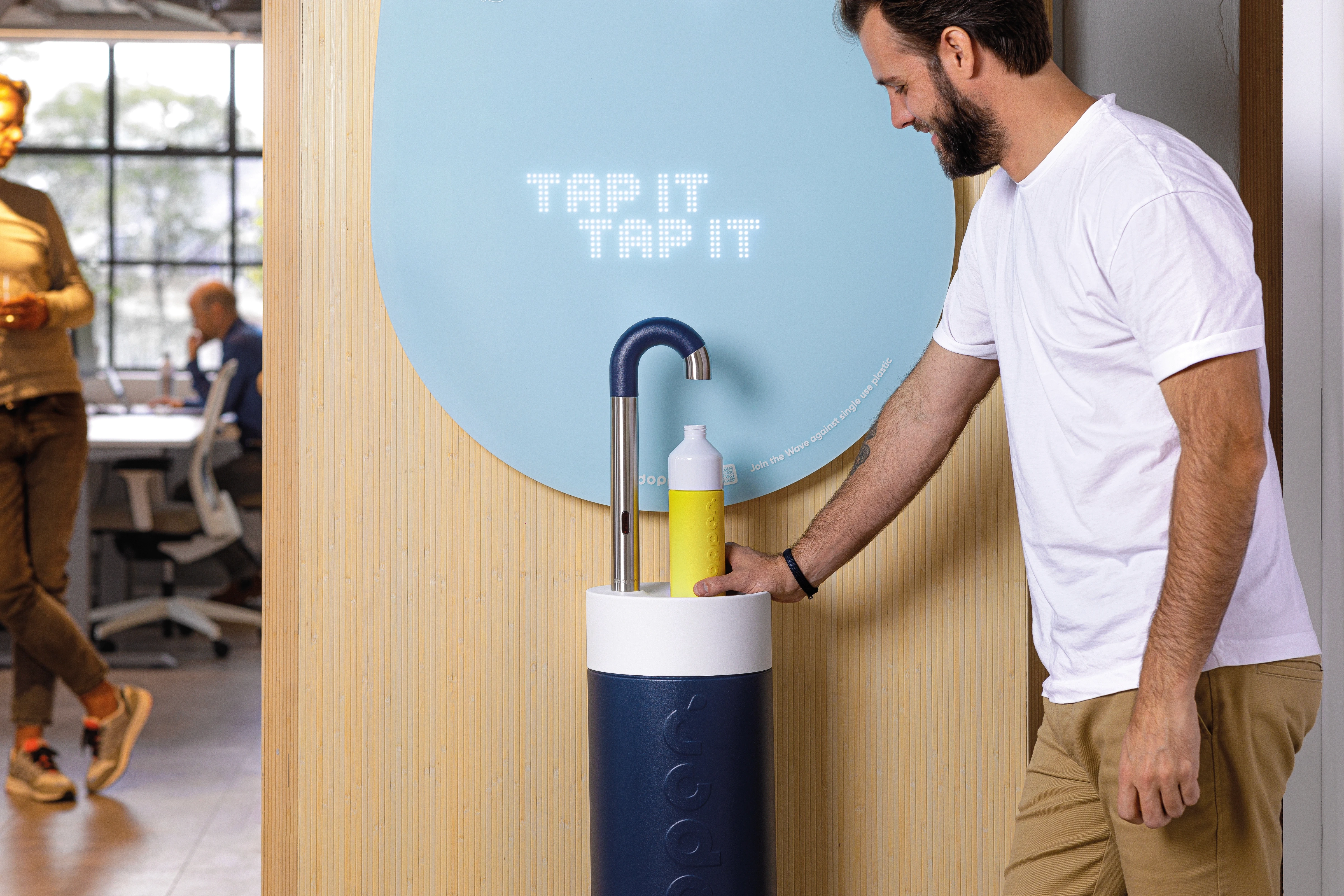
The Talking Tap
Dopper
The water tap designed to change behaviour
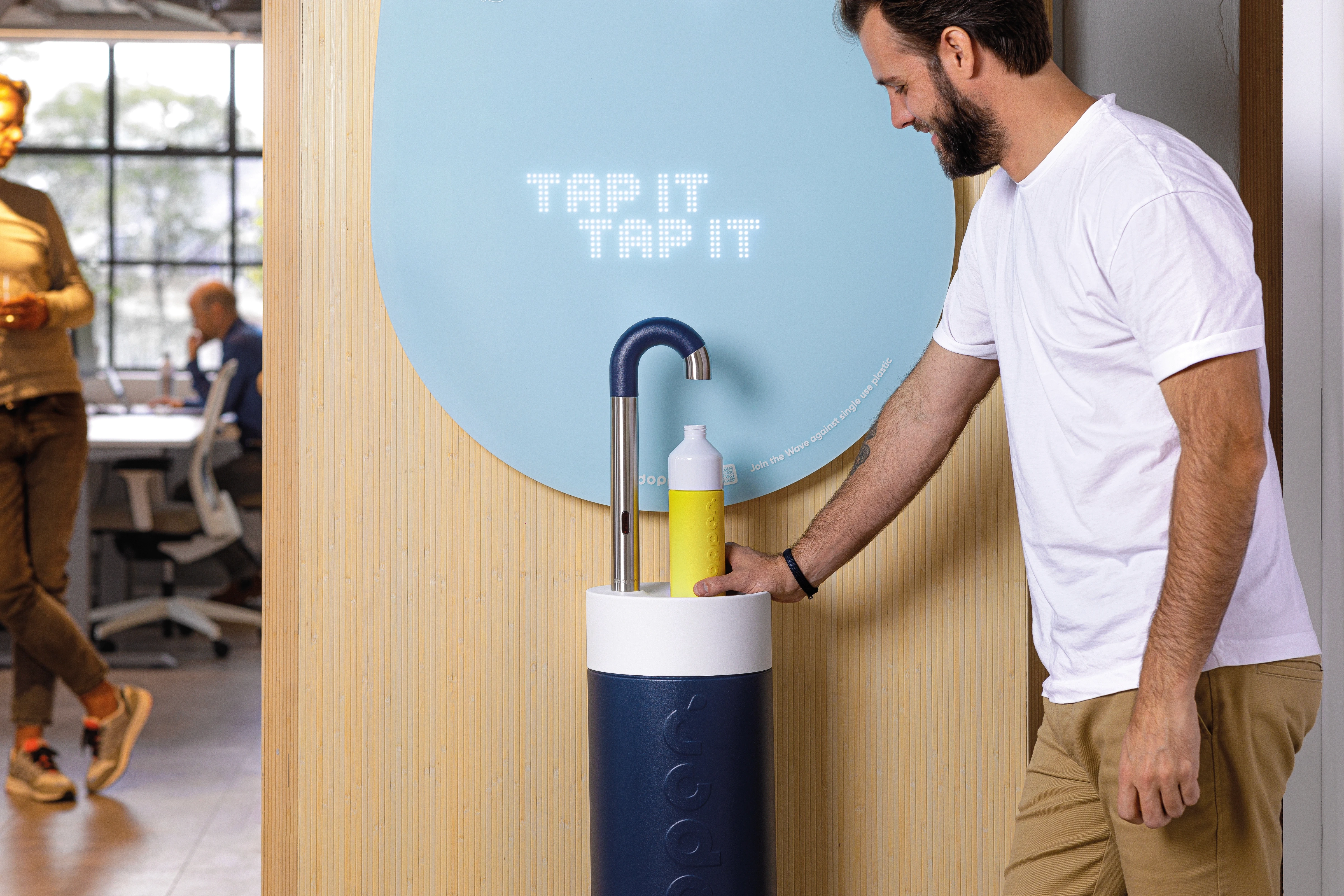
The Talking Tap
Dopper
The water tap designed to change behaviour
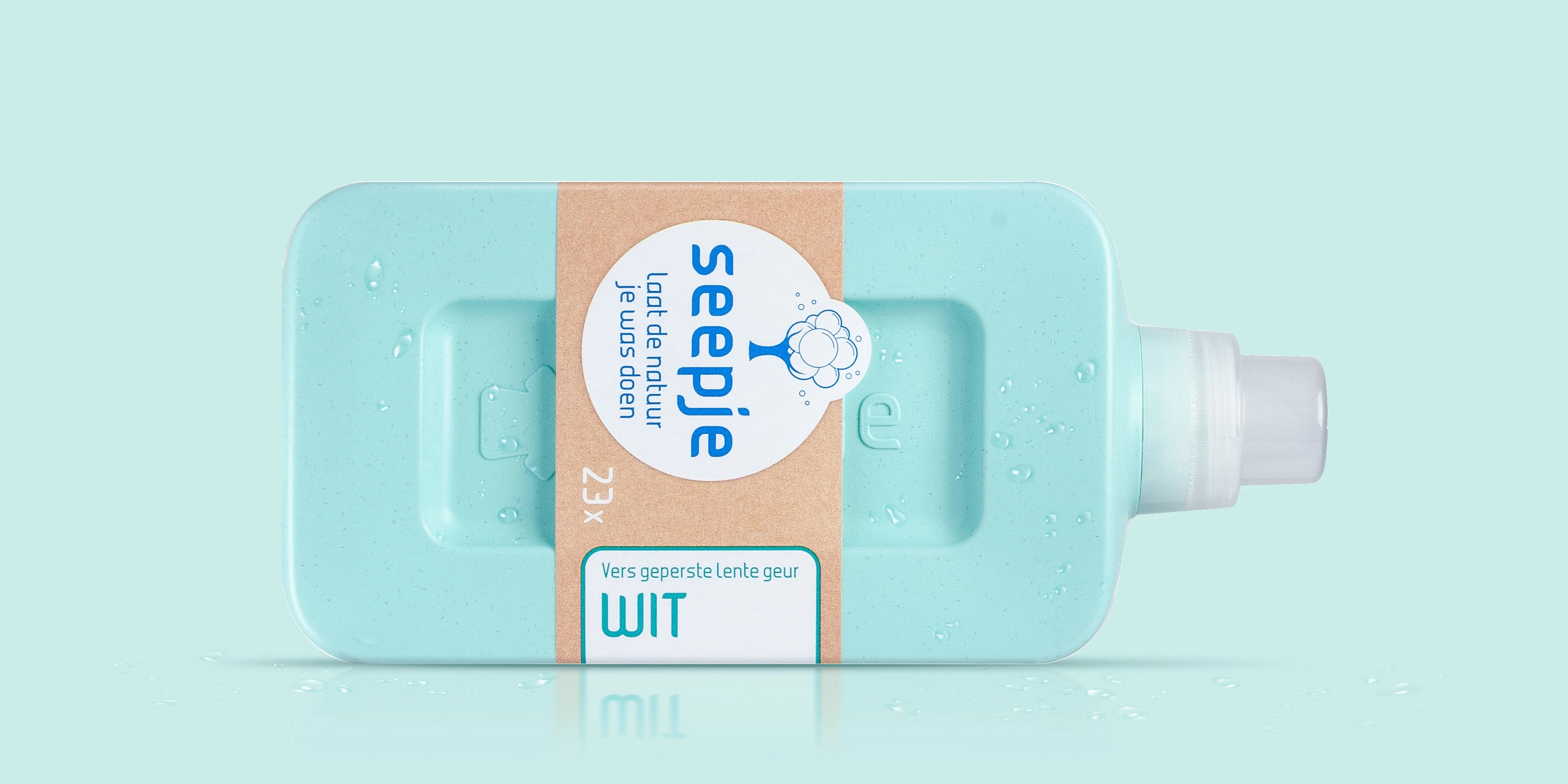
Sustainable Soap Packaging
Seepje
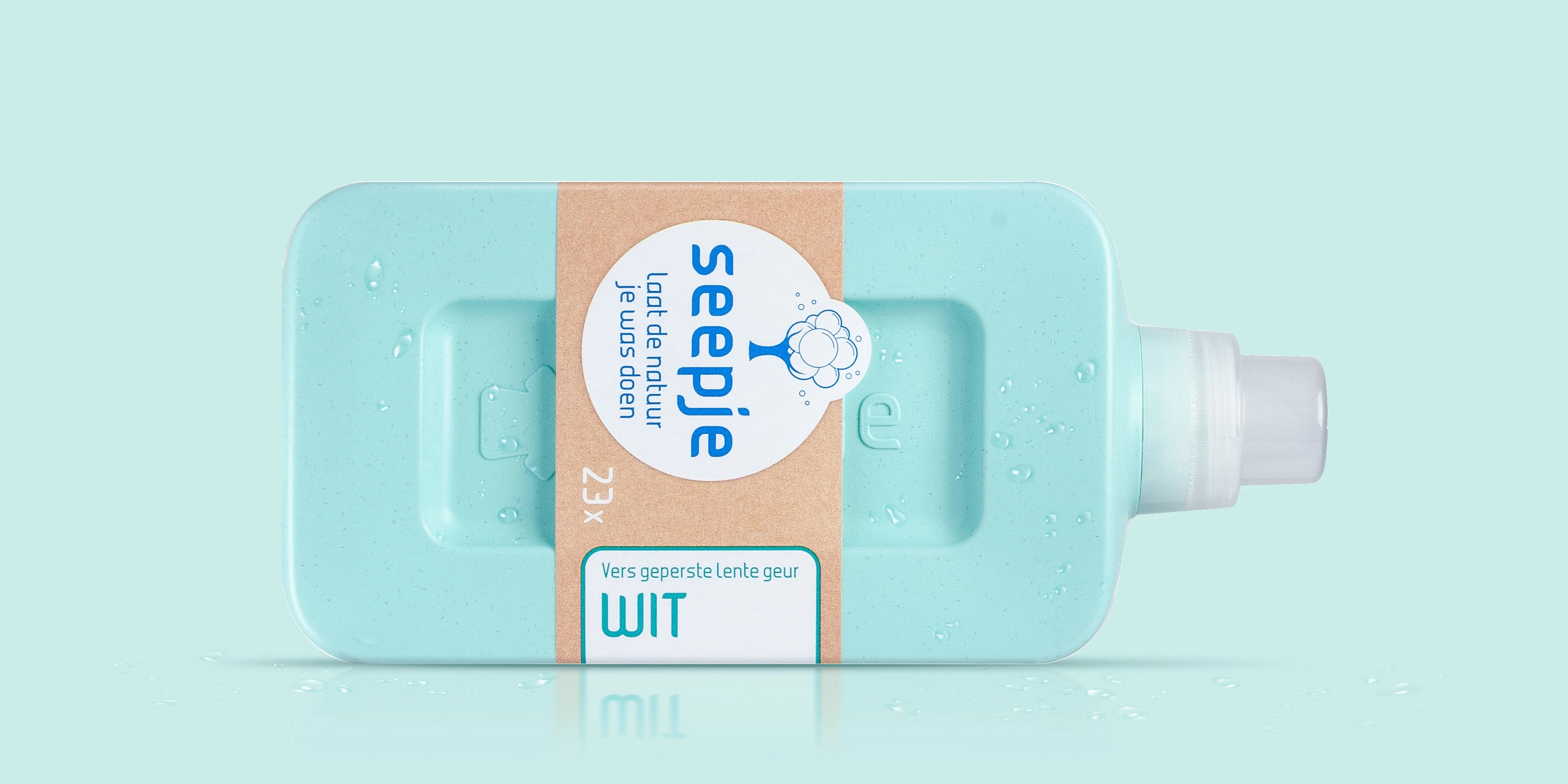
Sustainable Soap Packaging
Seepje
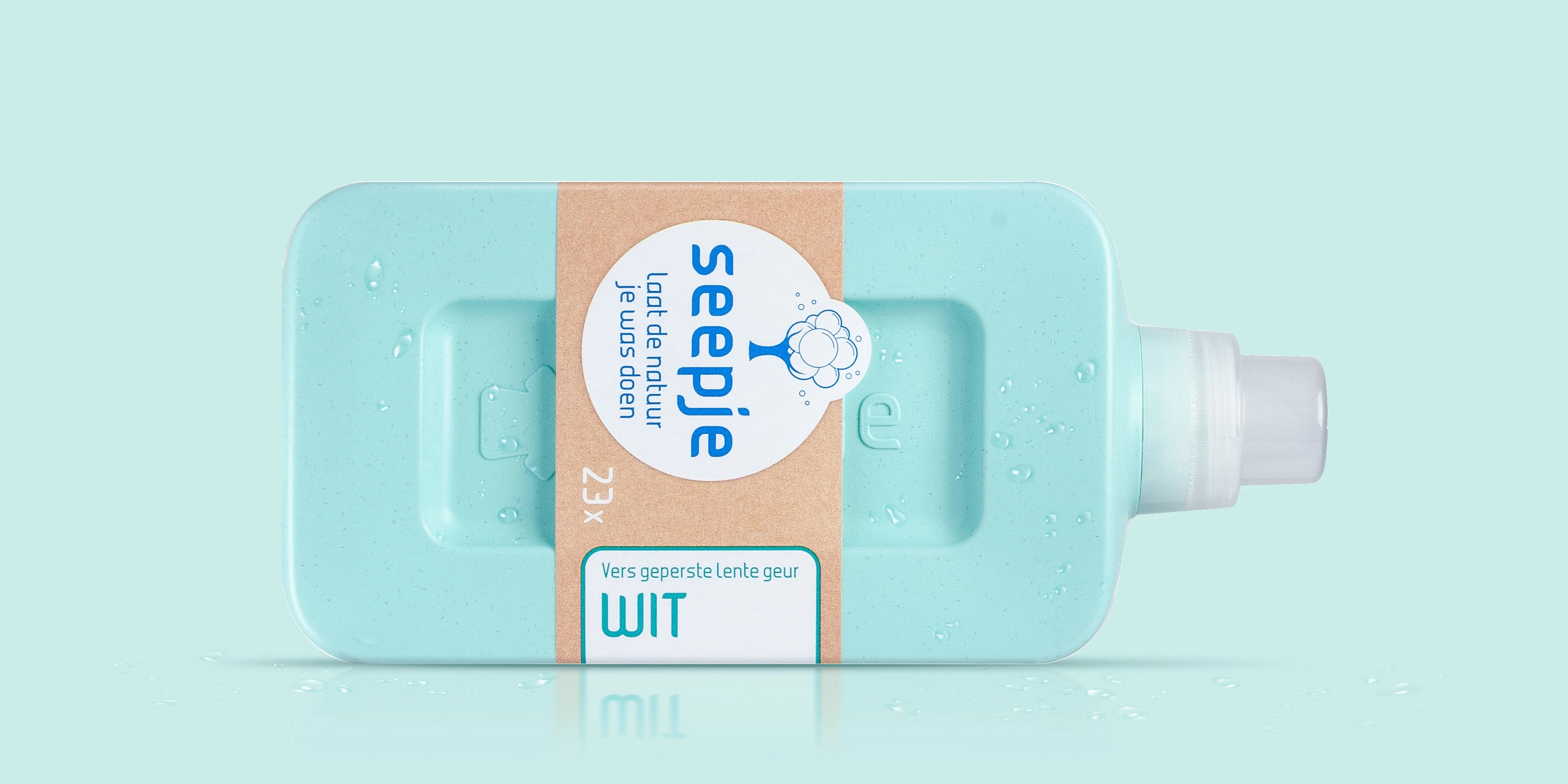
Sustainable Soap Packaging
Seepje
Telling the story of sustainable soap
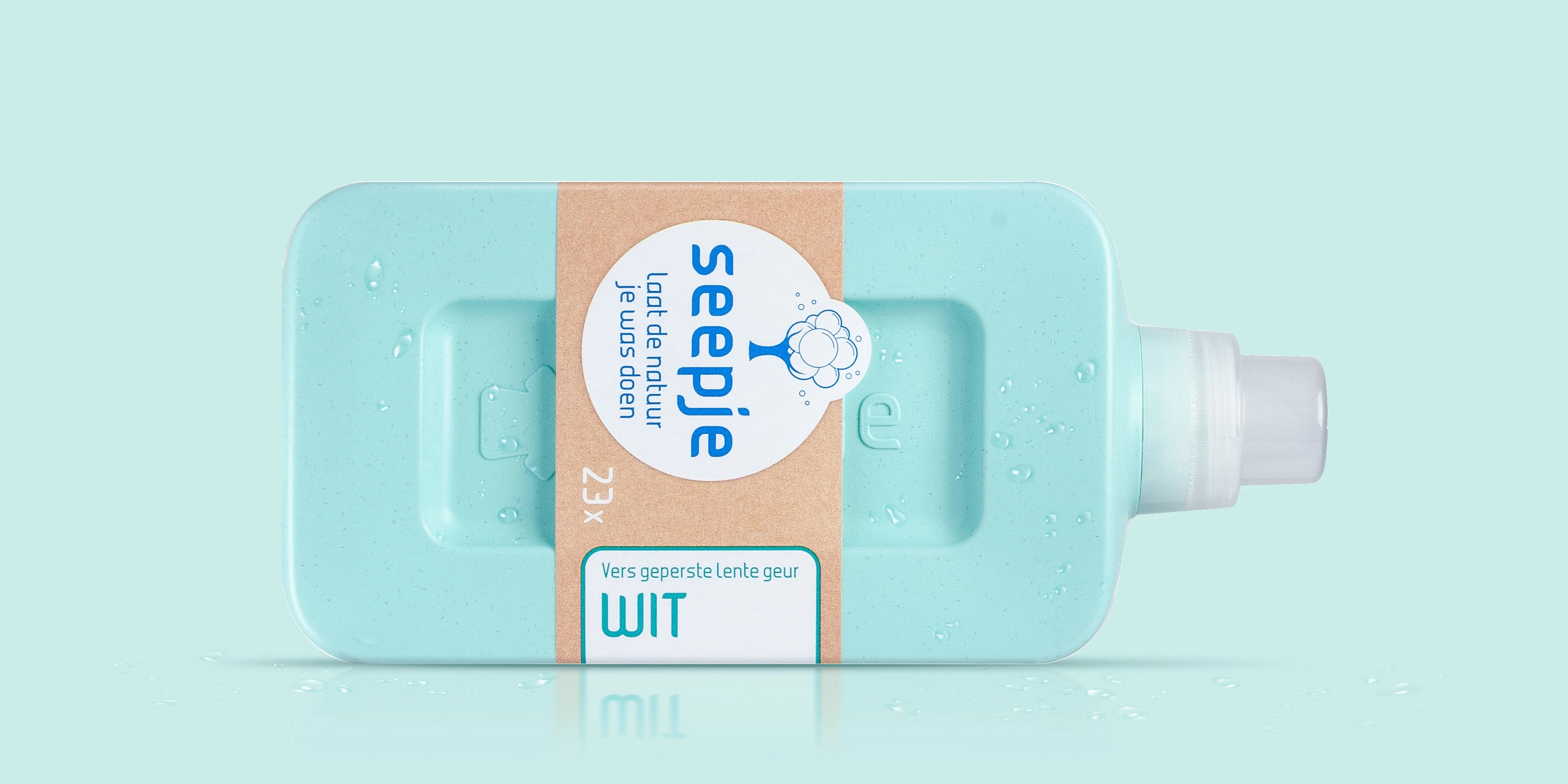
Sustainable Soap Packaging
Seepje
Telling the story of sustainable soap
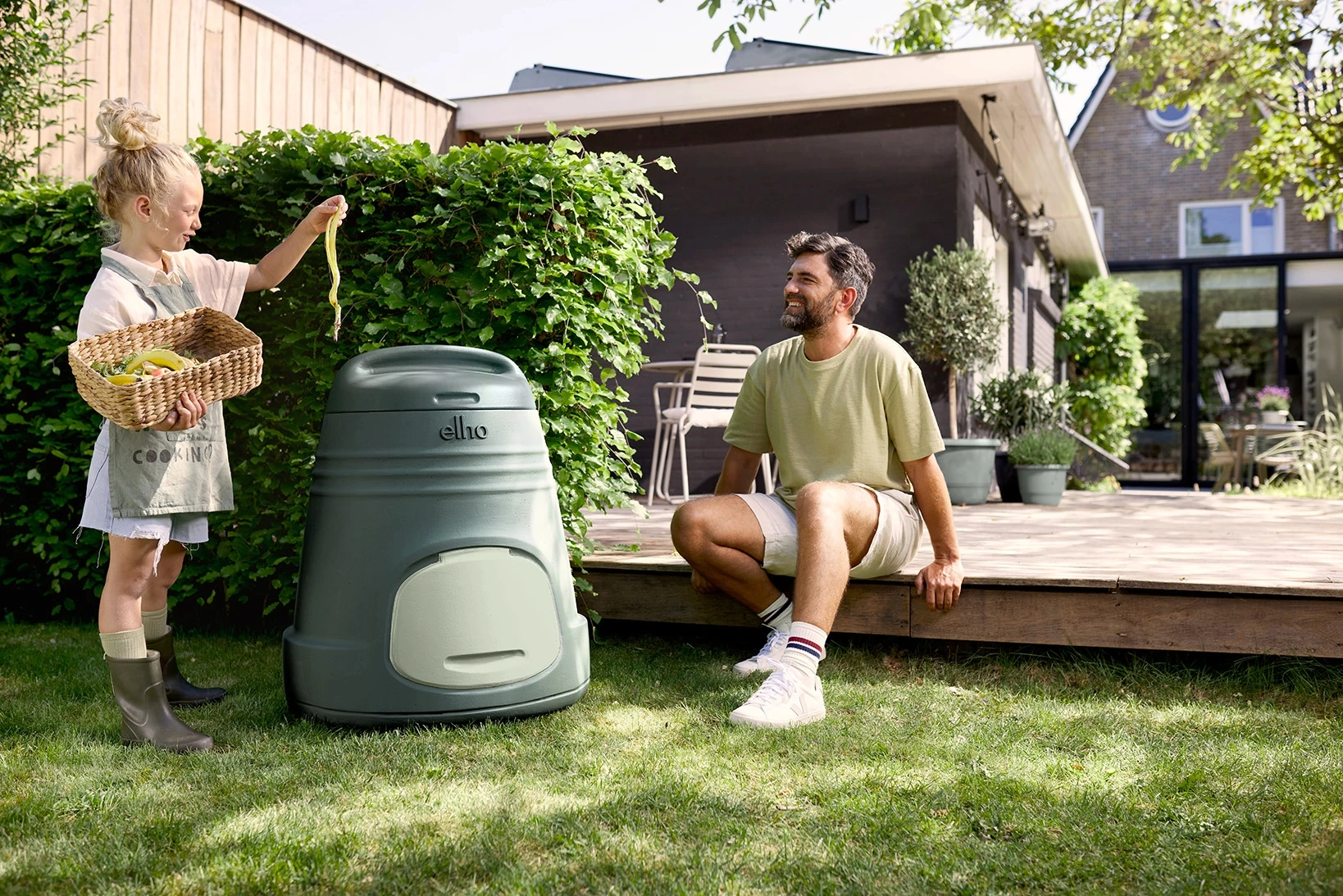
200L Home Composter
elho
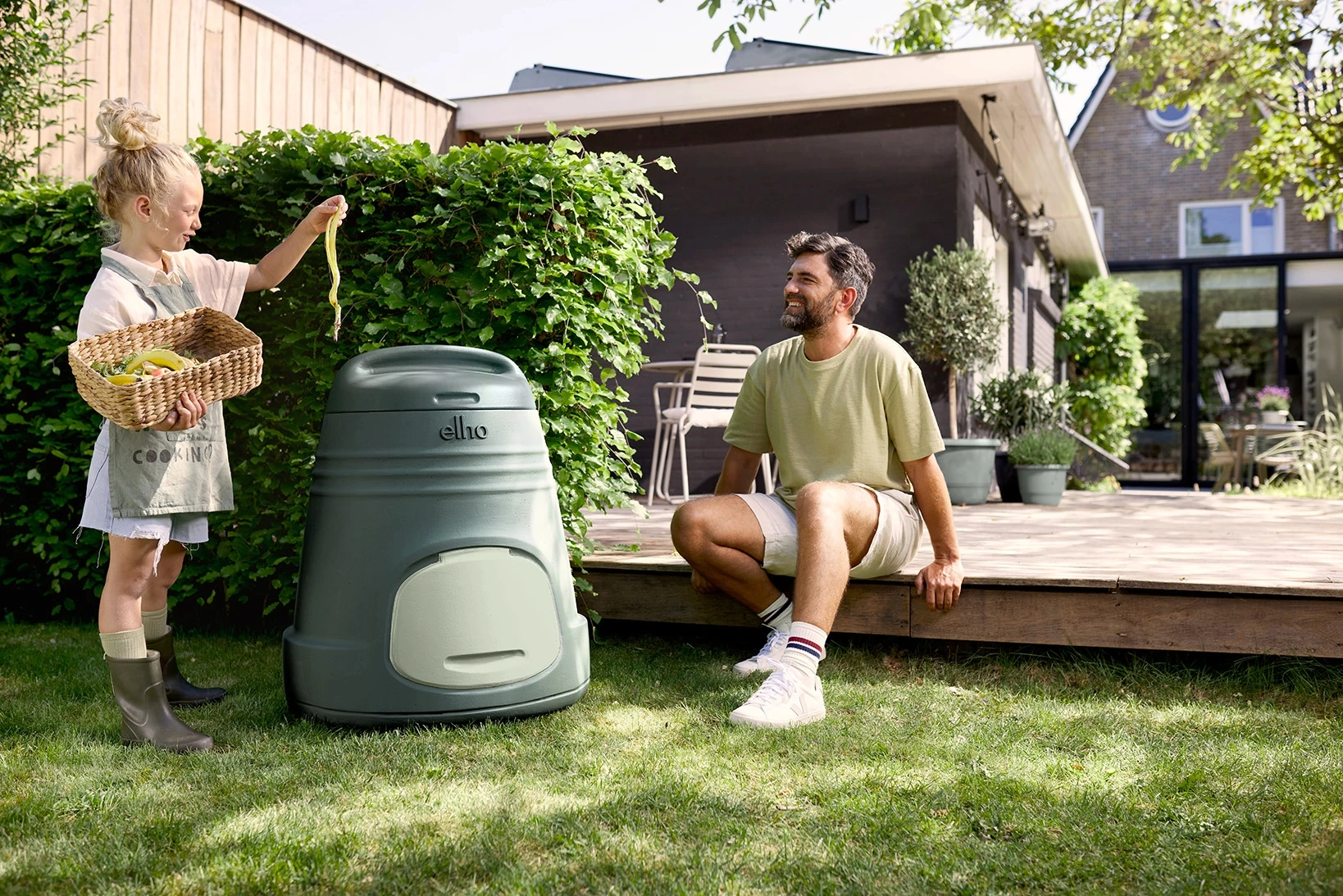
200L Home Composter
elho
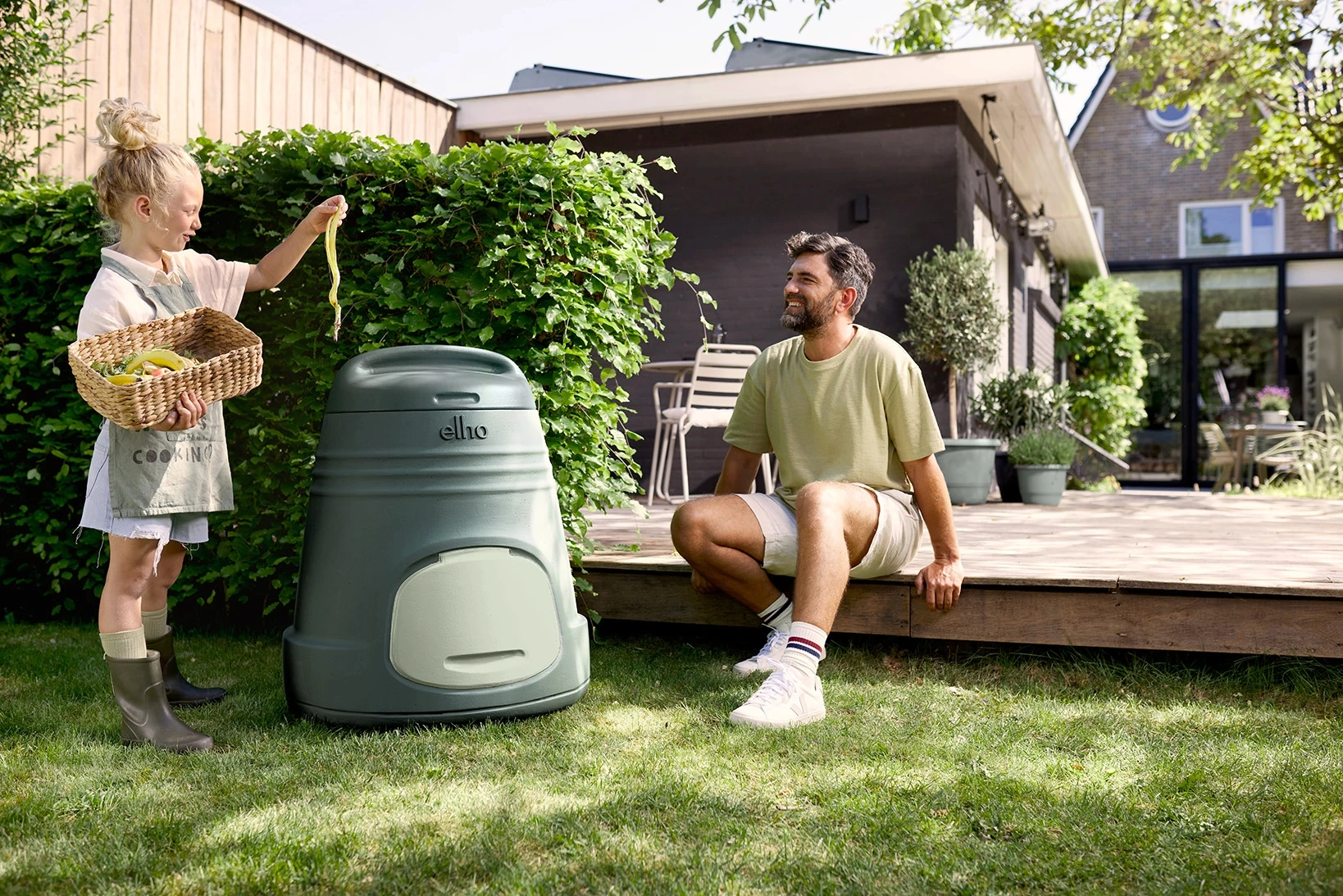
200L Home Composter
elho
Inspiring consumers to connect to nature
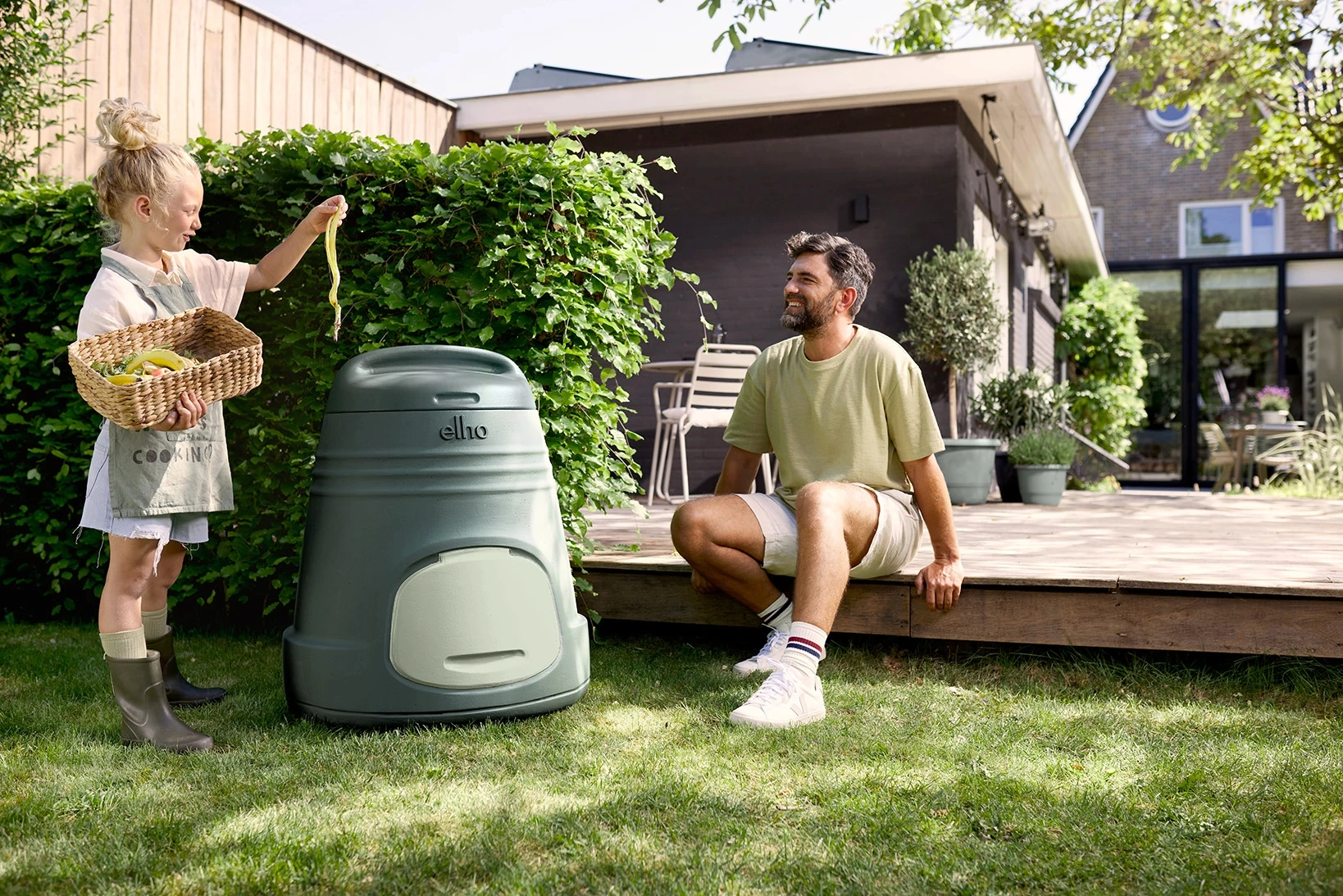
200L Home Composter
elho
Inspiring consumers to connect to nature
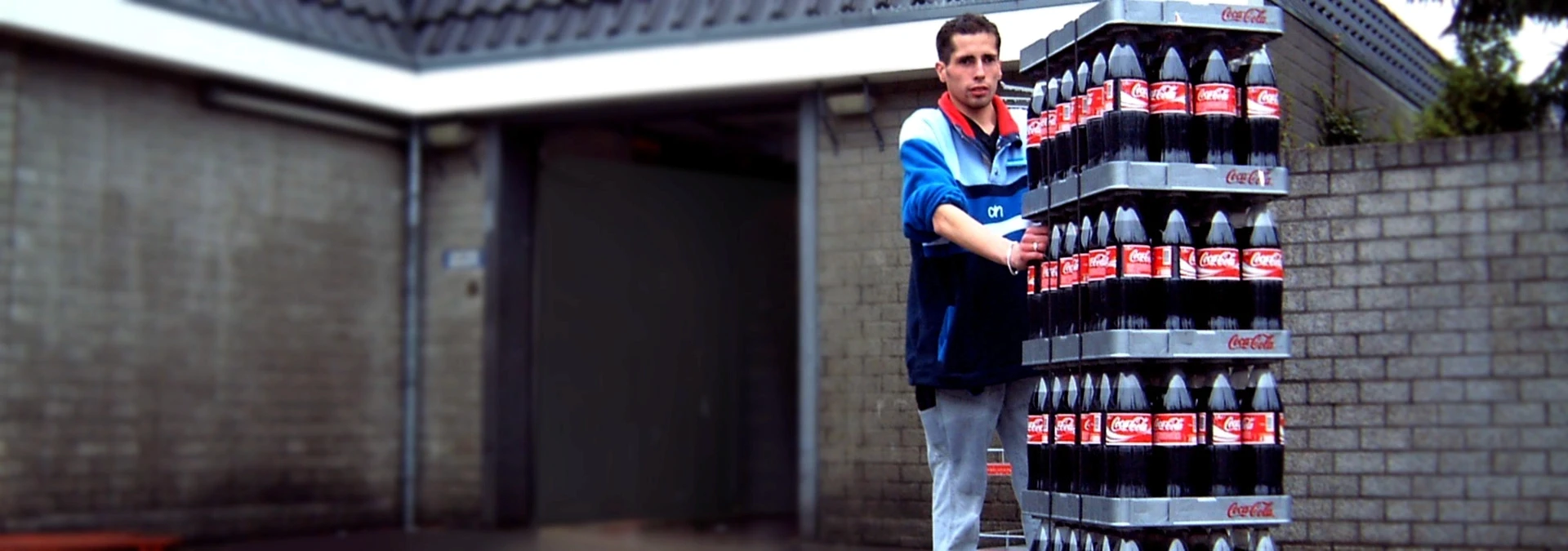
Returnable Soft Drink Tray
Albert Heijn + Coca-Cola
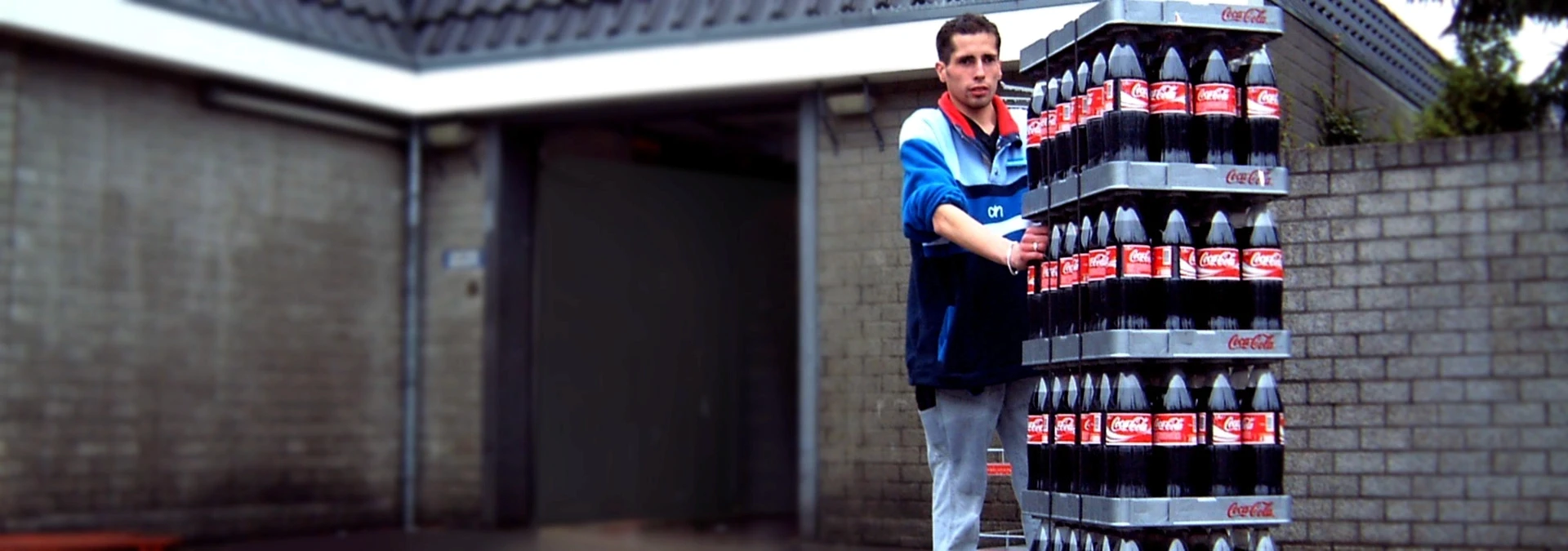
Returnable Soft Drink Tray
Albert Heijn + Coca-Cola
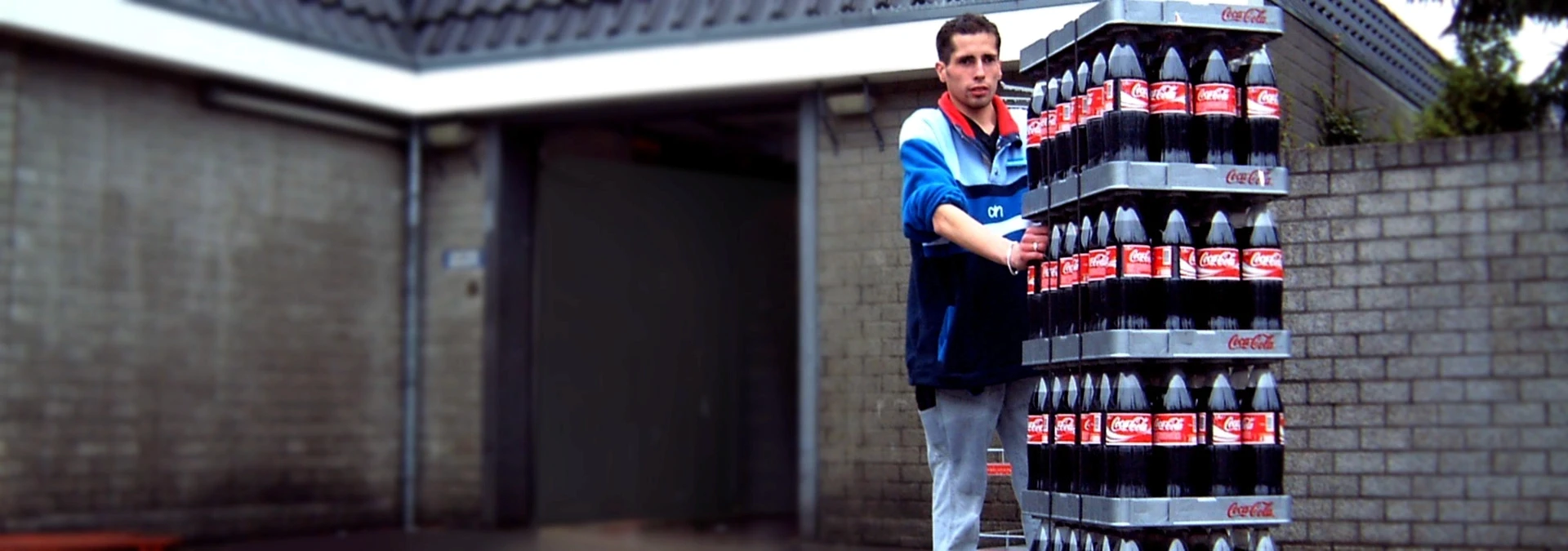
Returnable Soft Drink Tray
Albert Heijn + Coca-Cola
Effortless handling saving time, cost and resources
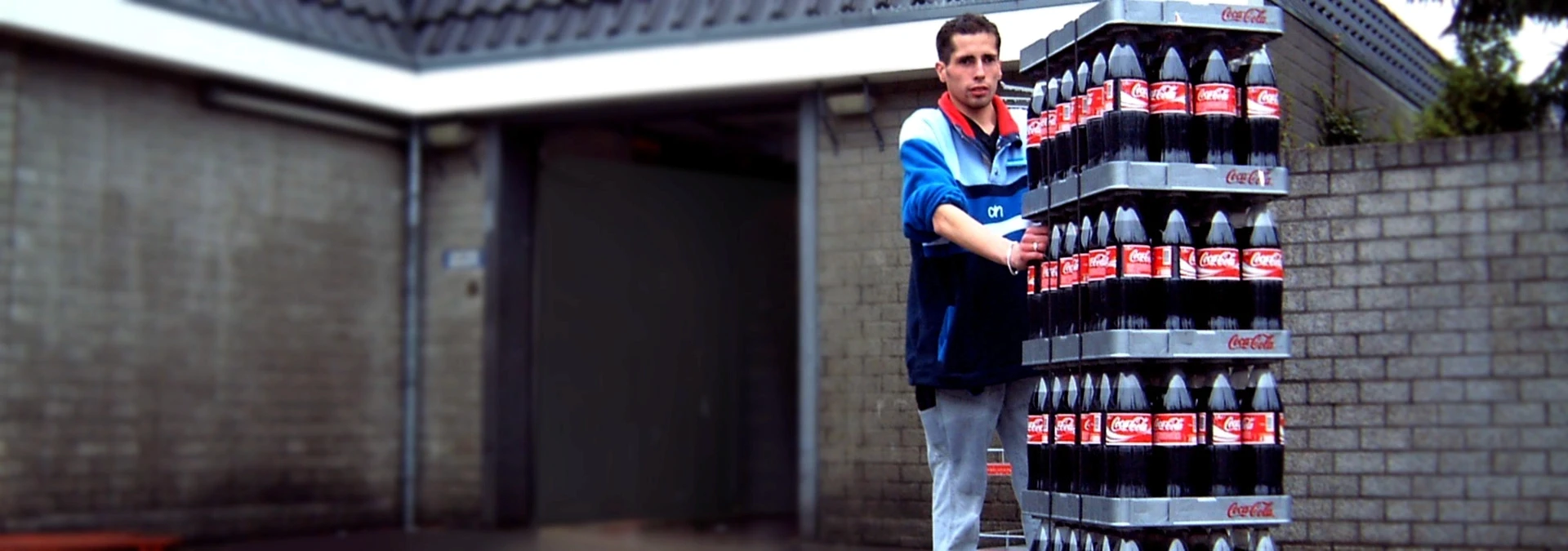
Returnable Soft Drink Tray
Albert Heijn + Coca-Cola
Effortless handling saving time, cost and resources
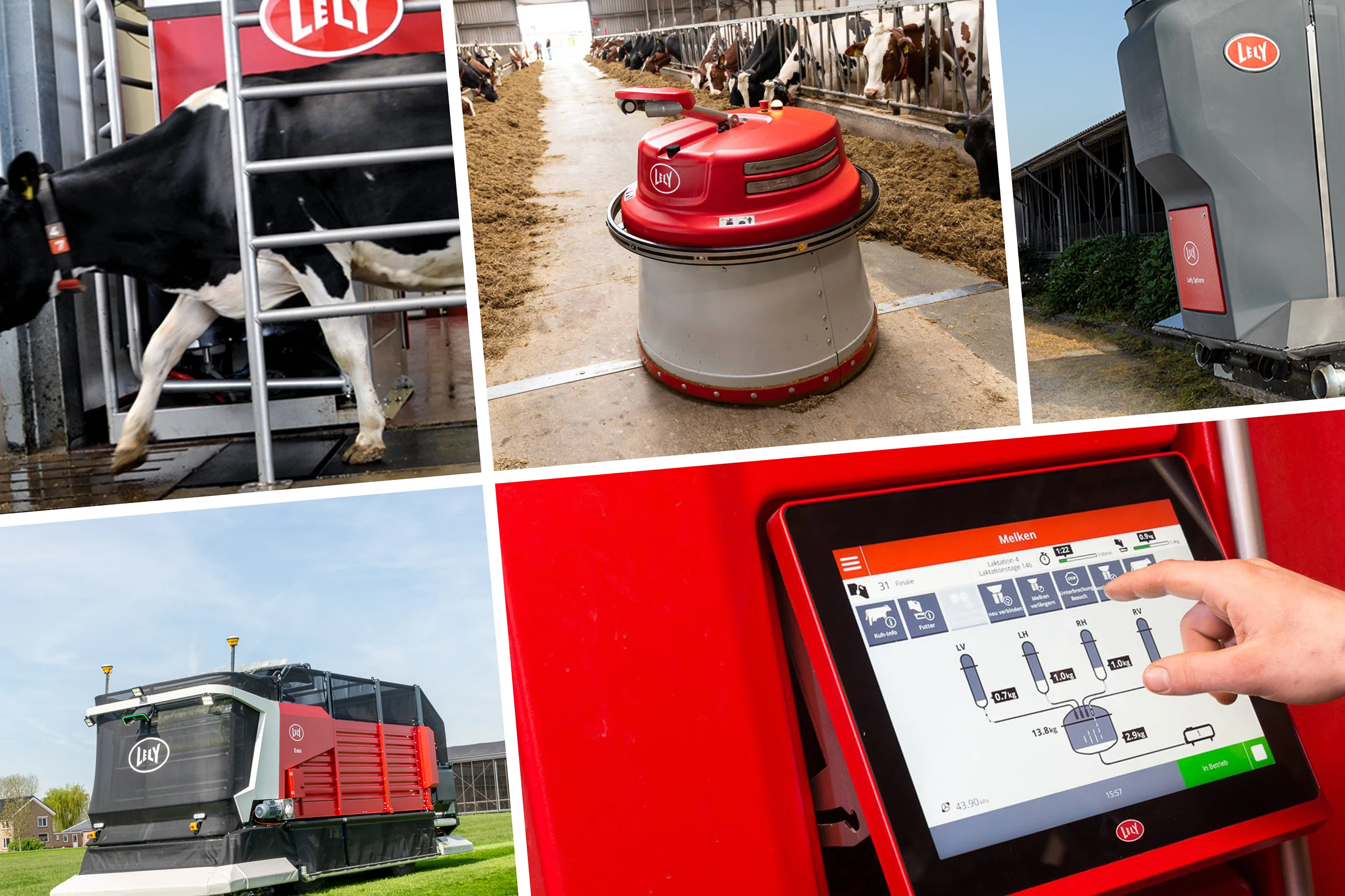
Red Rules
Lely
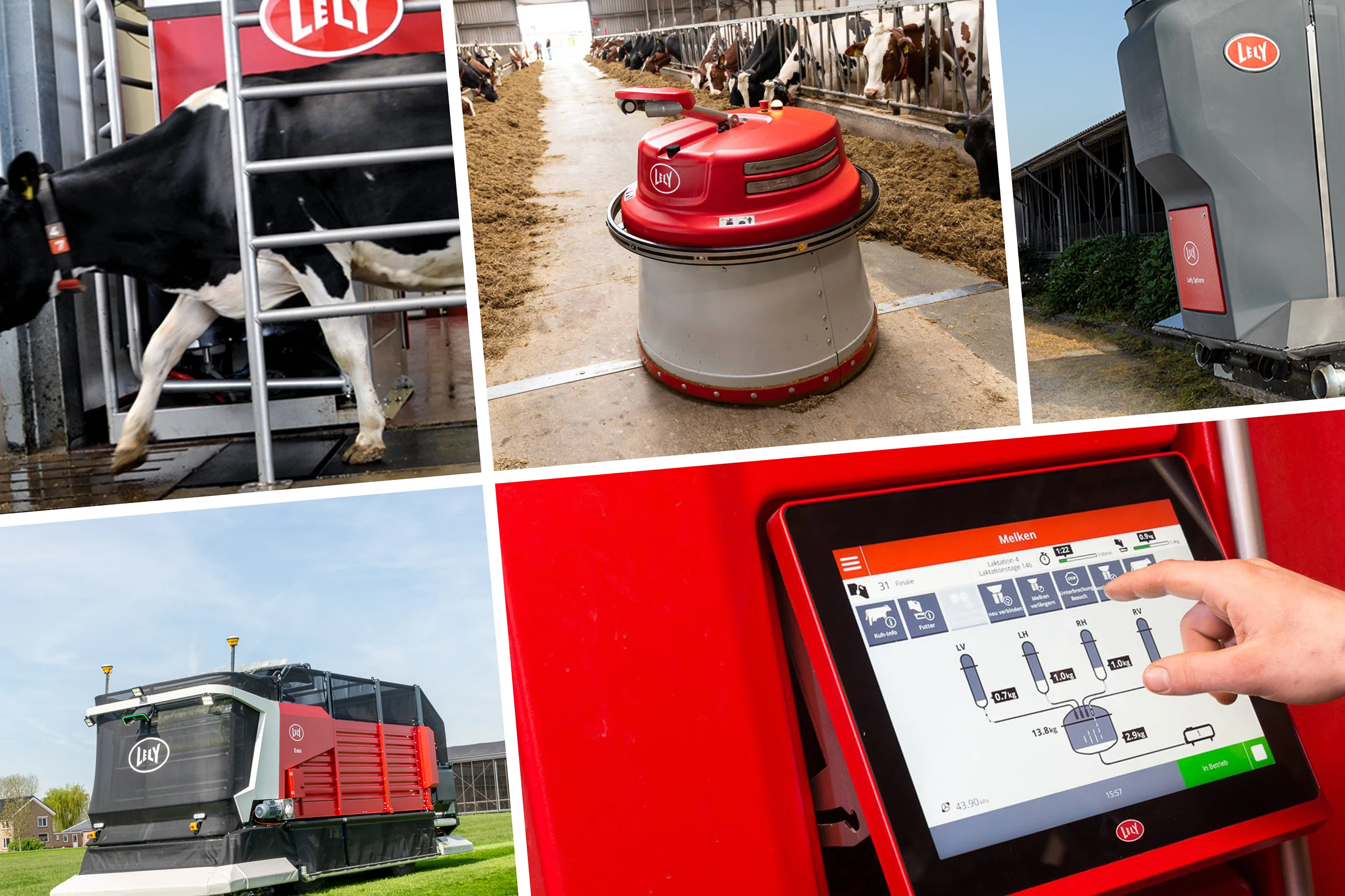
Red Rules
Lely
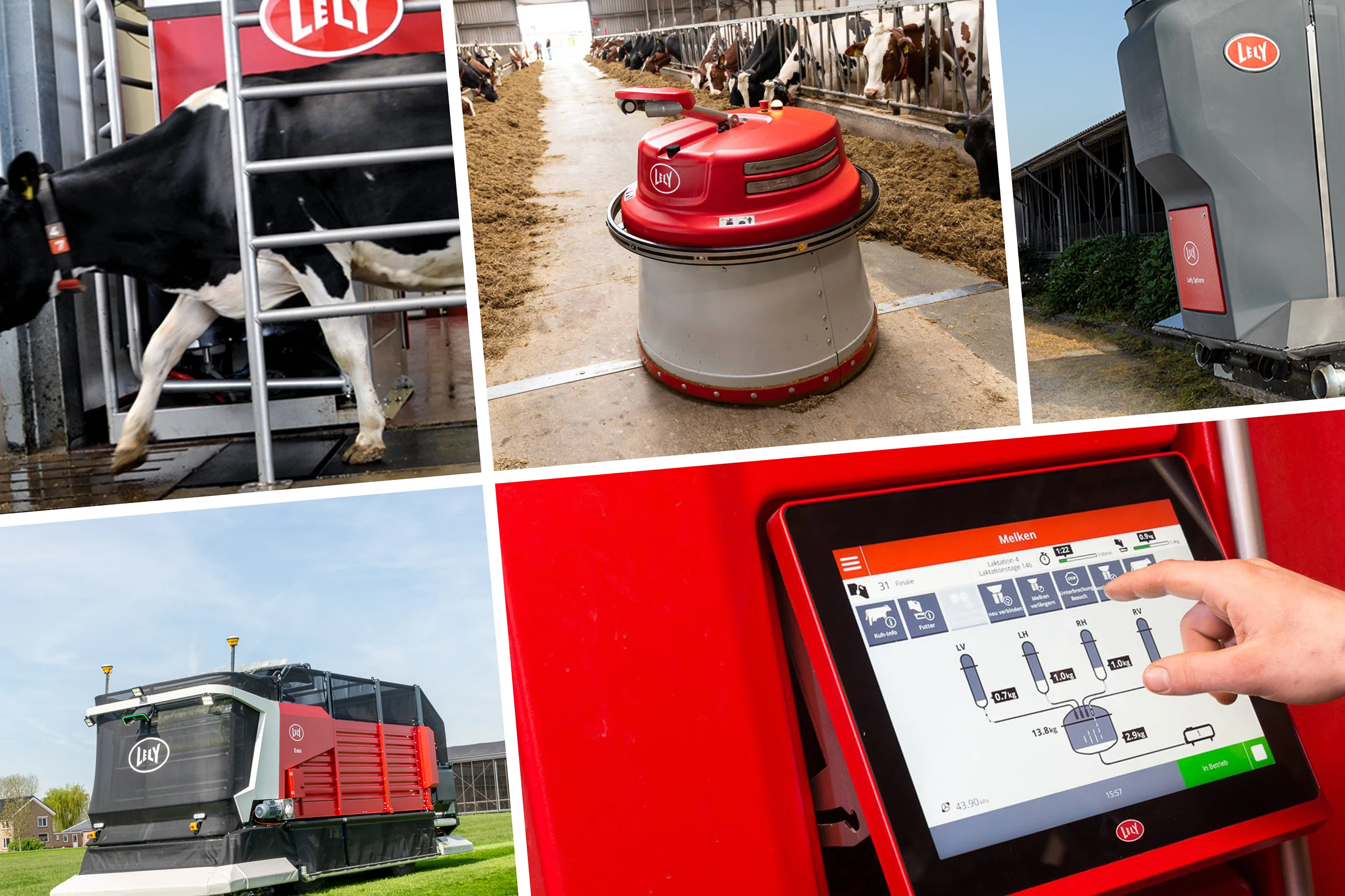
Red Rules
Lely
Design guidelines for the smart farm
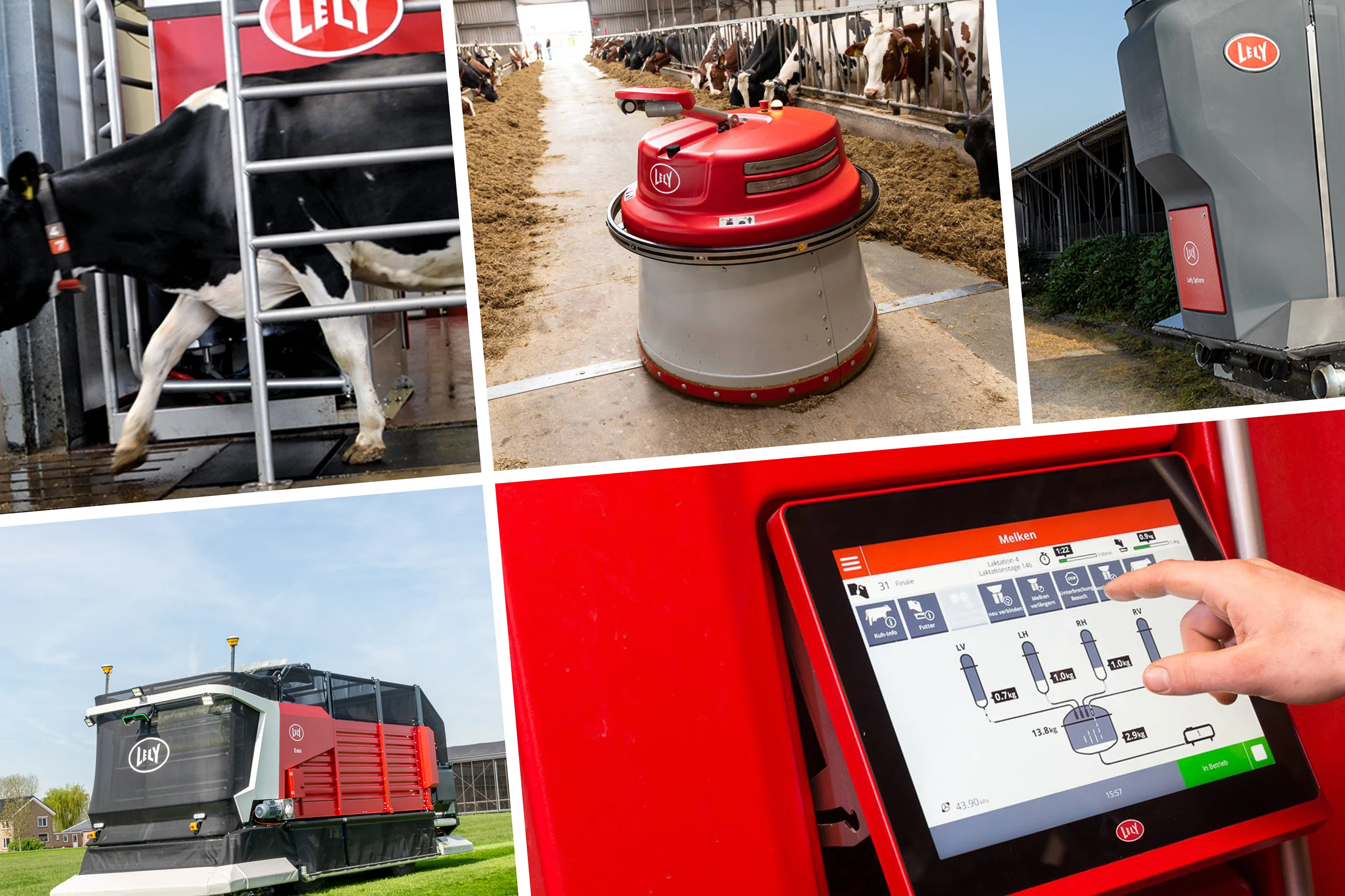
Red Rules
Lely
Design guidelines for the smart farm
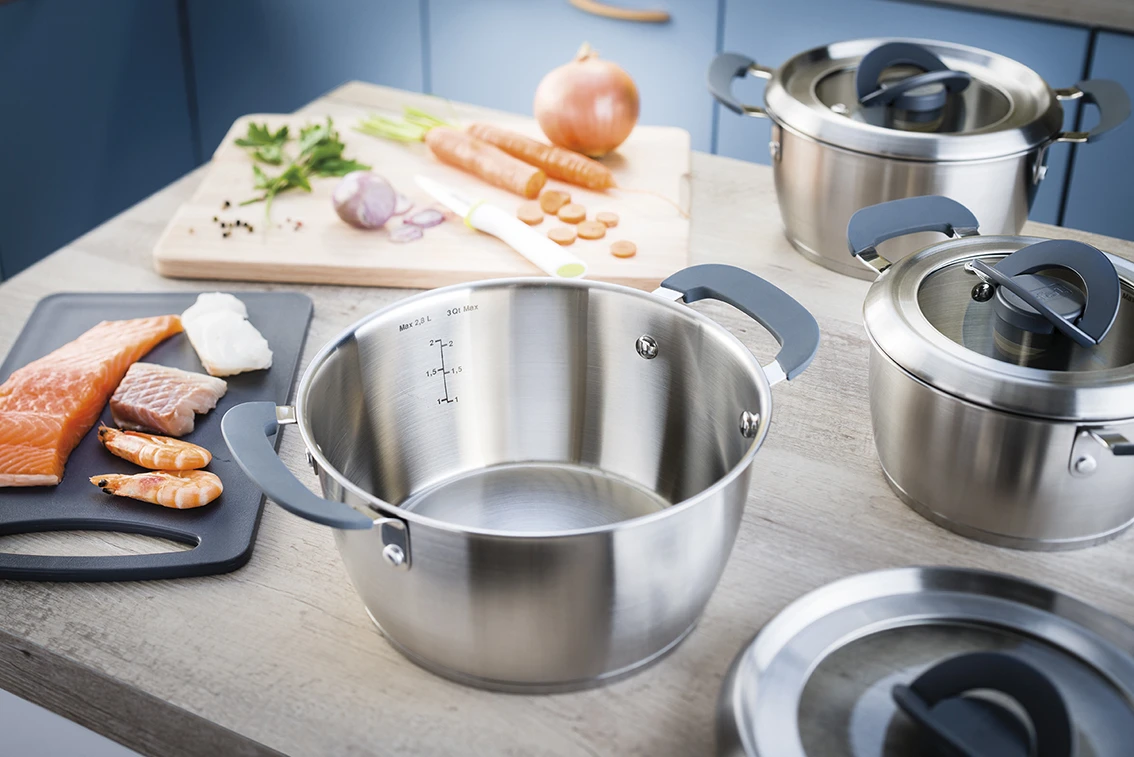
Tefal Clever Cookware
Groupe SEB
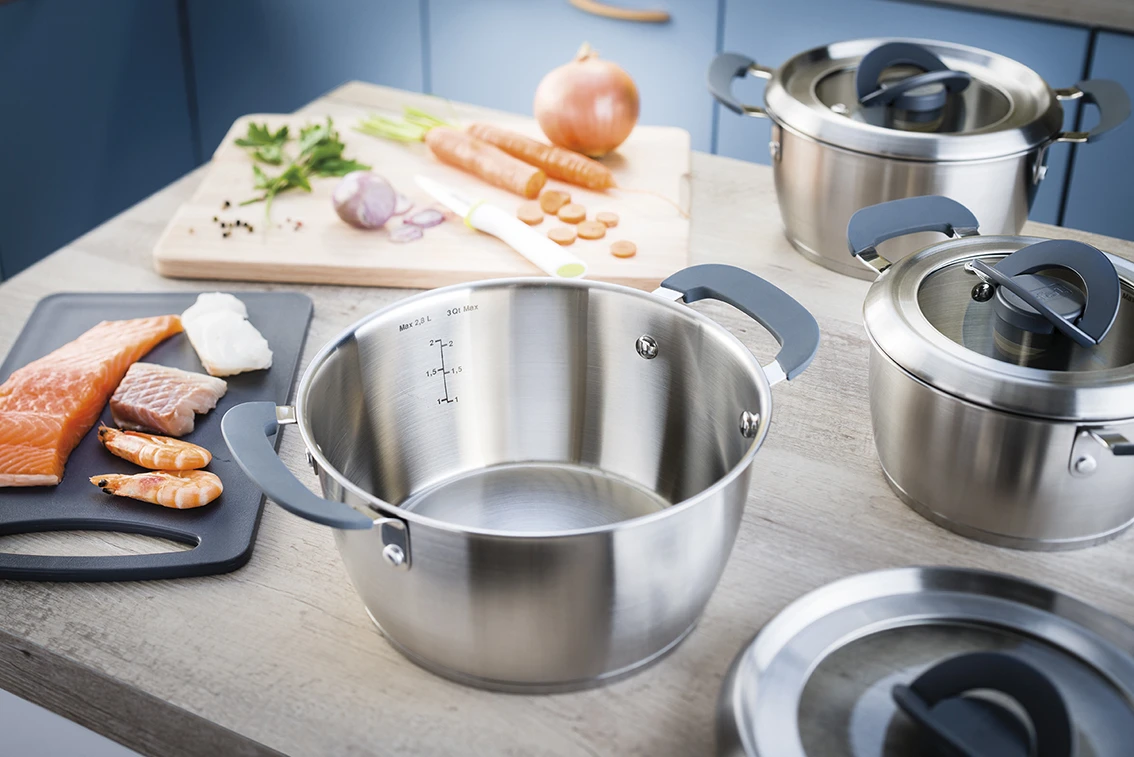
Tefal Clever Cookware
Groupe SEB
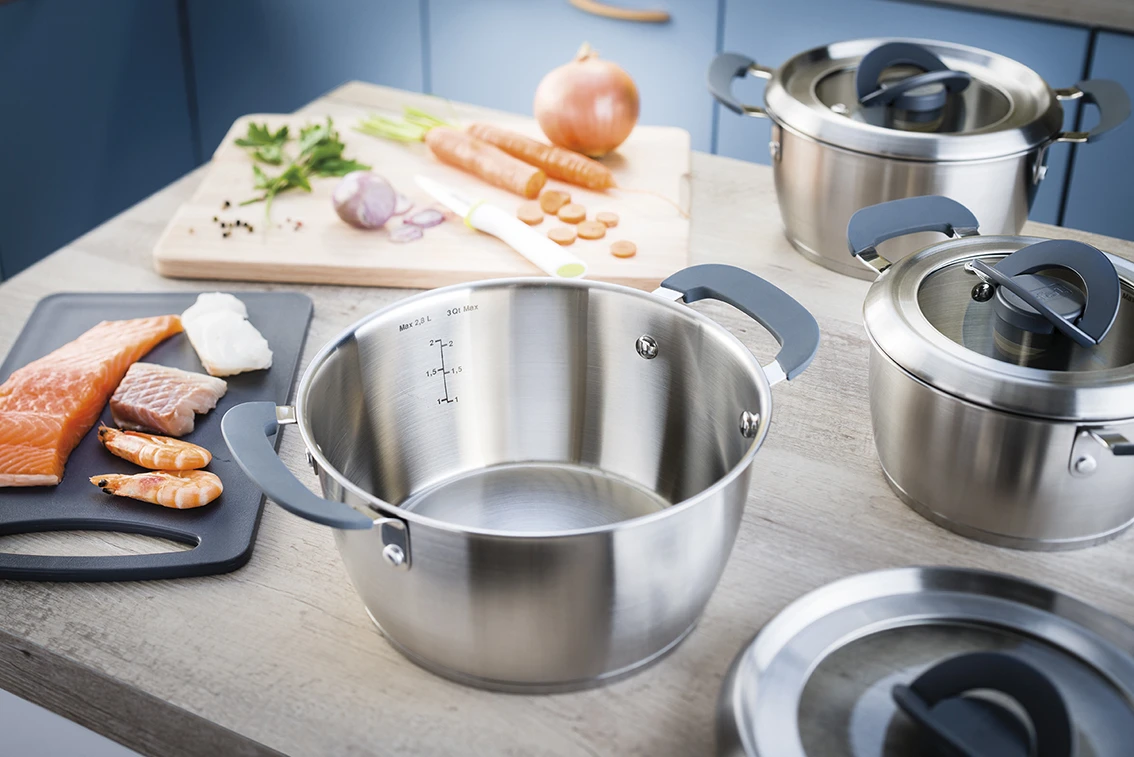
Tefal Clever Cookware
Groupe SEB
User-friendly solutions for healthy cooking
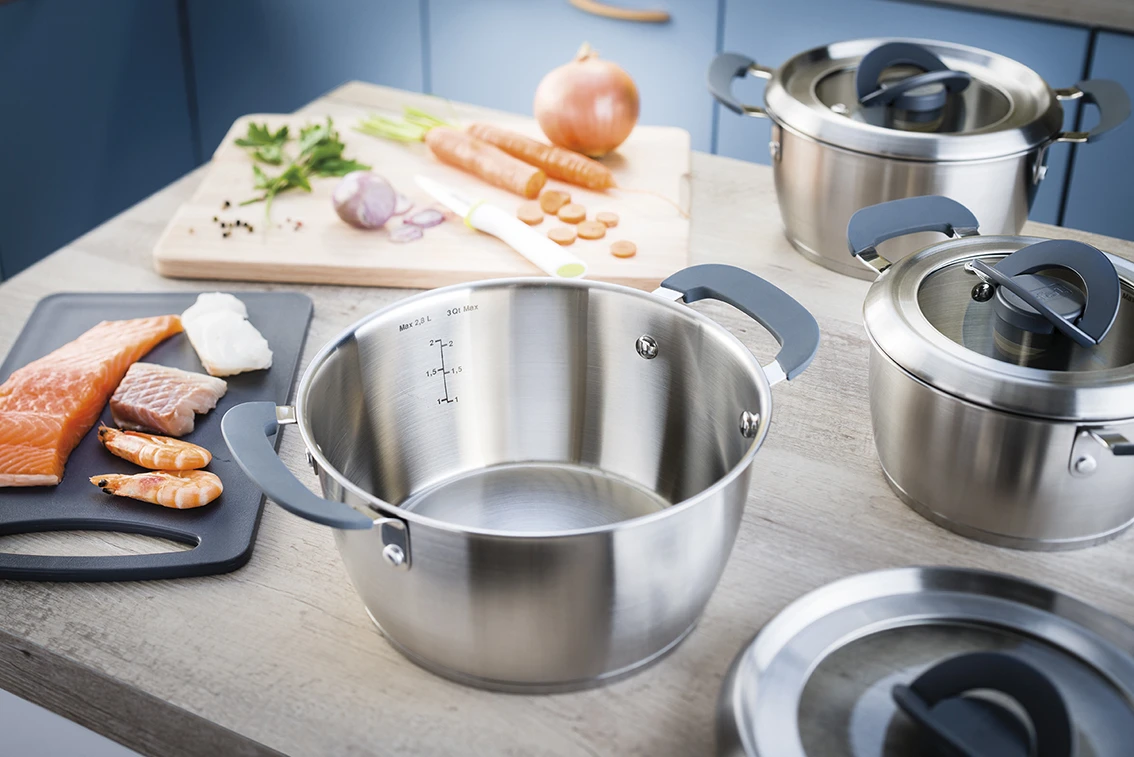
Tefal Clever Cookware
Groupe SEB
User-friendly solutions for healthy cooking
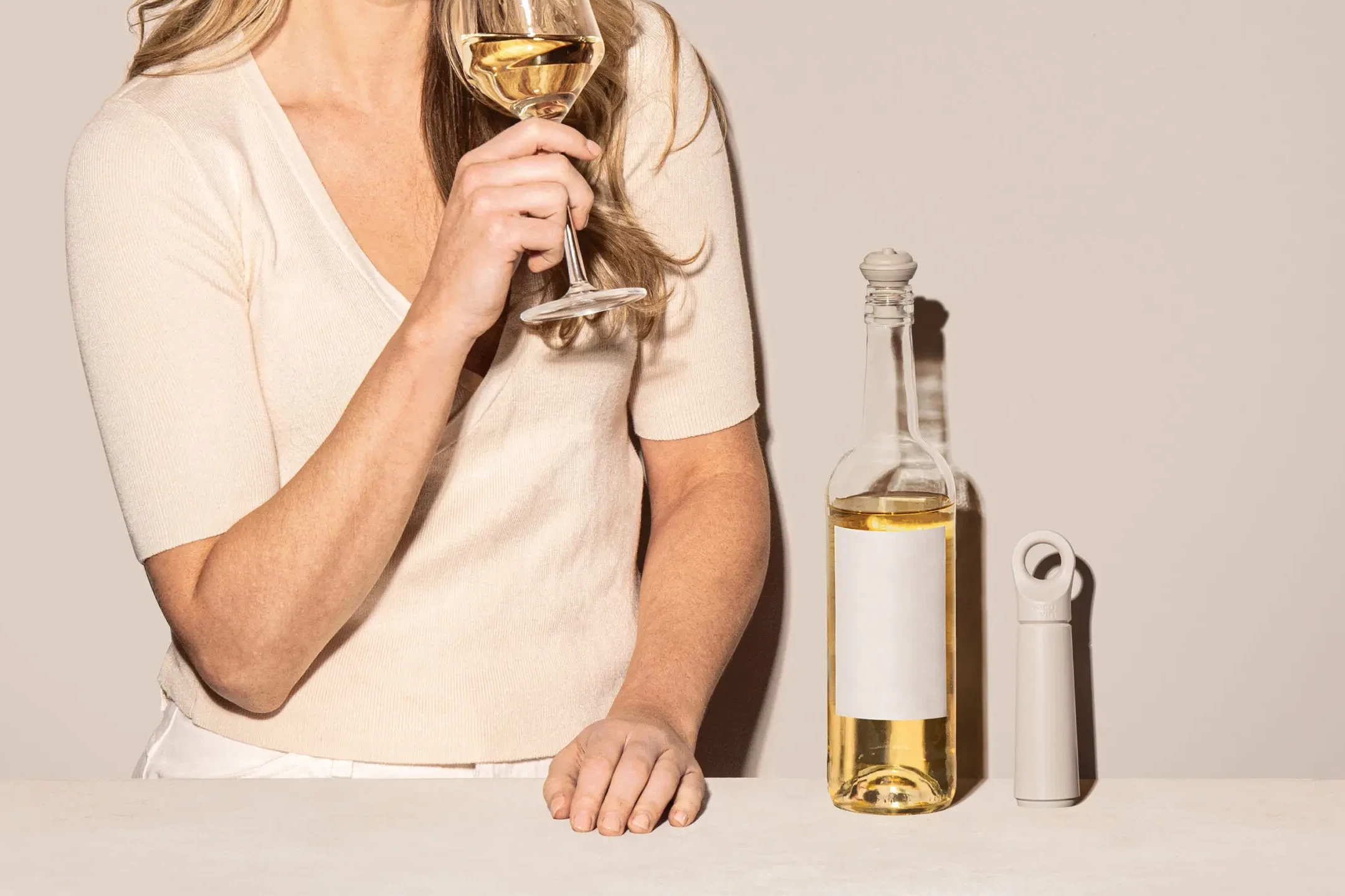
Loop Winesaver
Vacu Vin
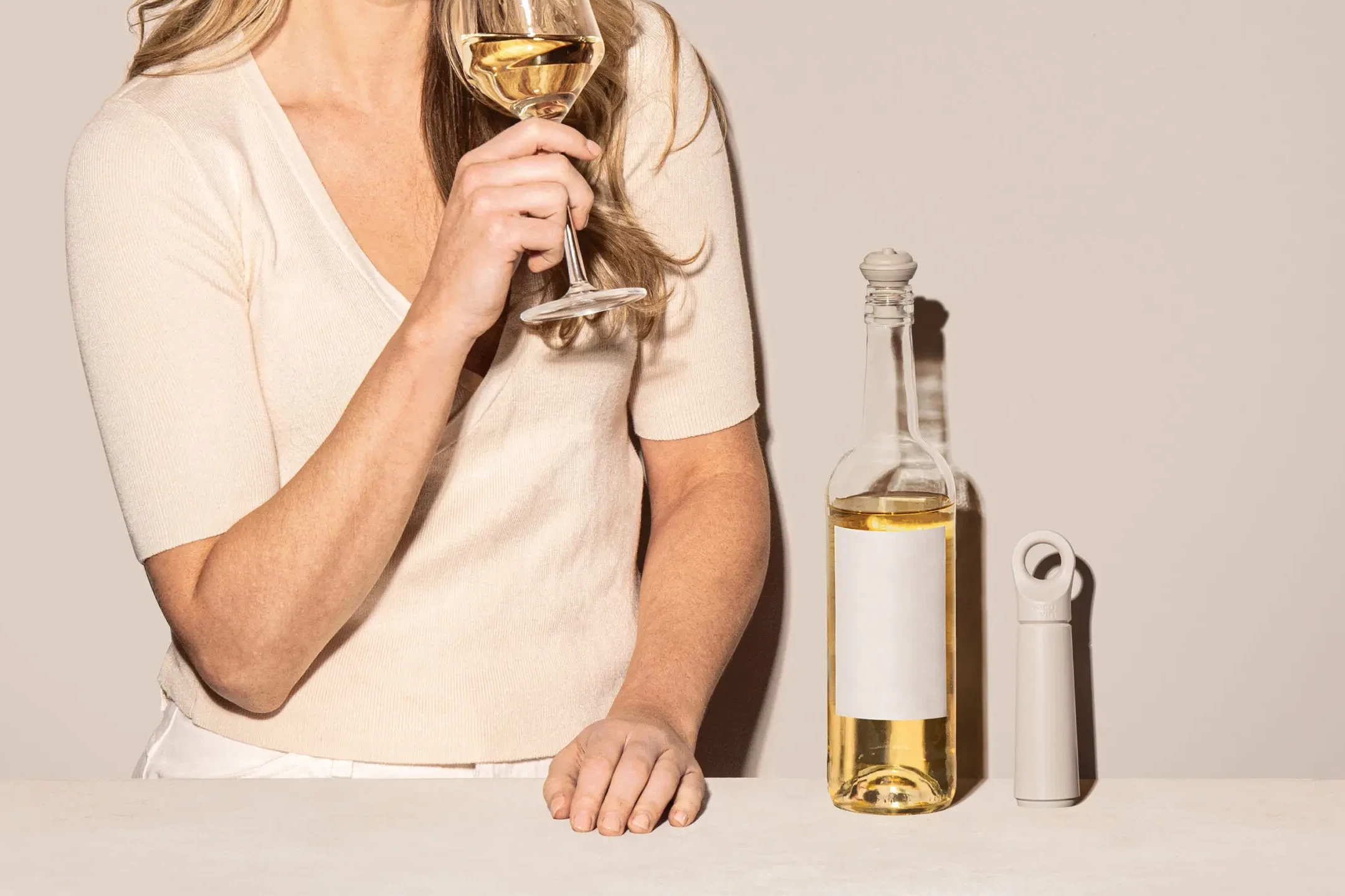
Loop Winesaver
Vacu Vin
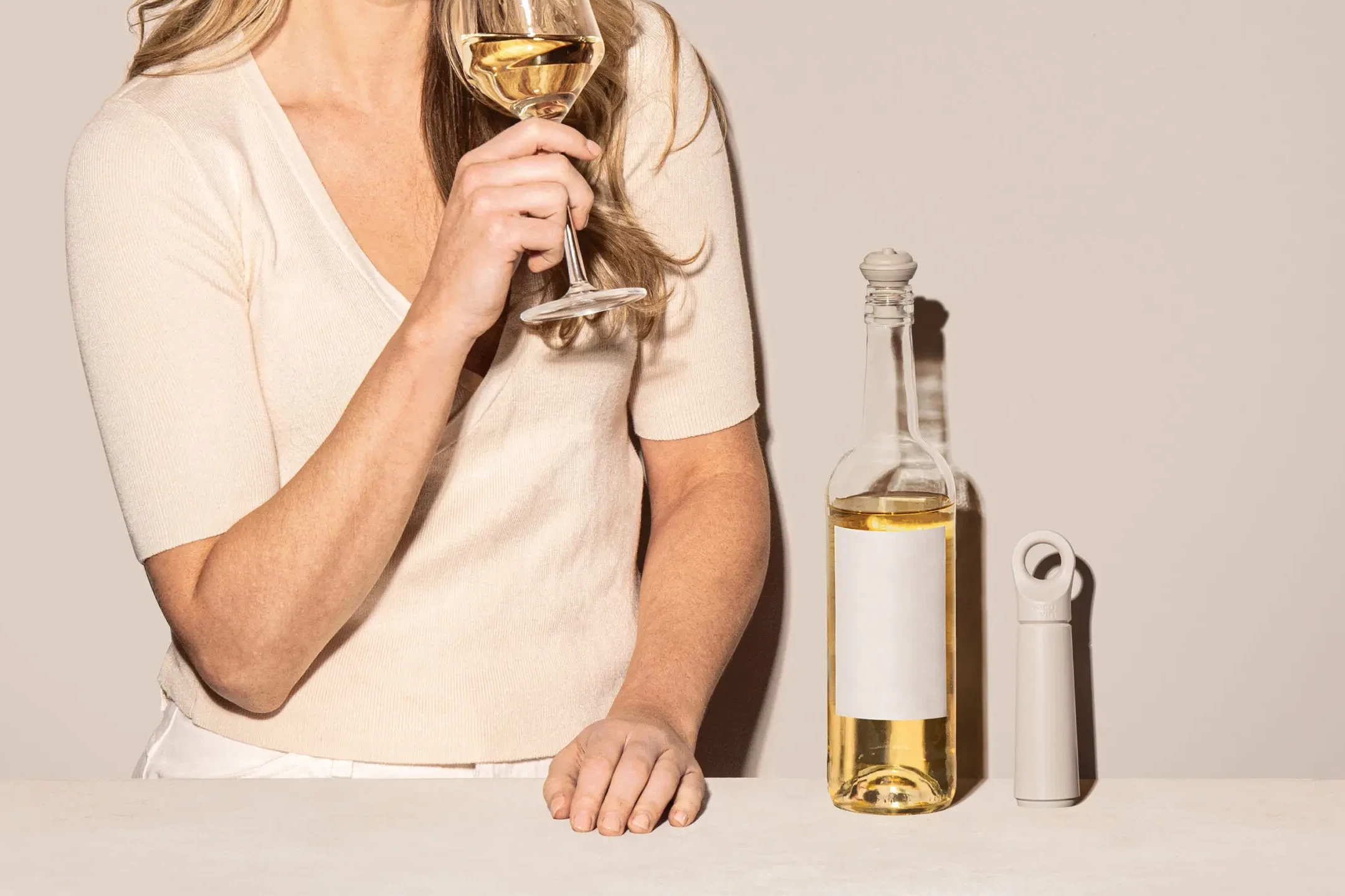
Loop Winesaver
Vacu Vin
Repositioning Vacu Vin: let the next gen enjoy every drop
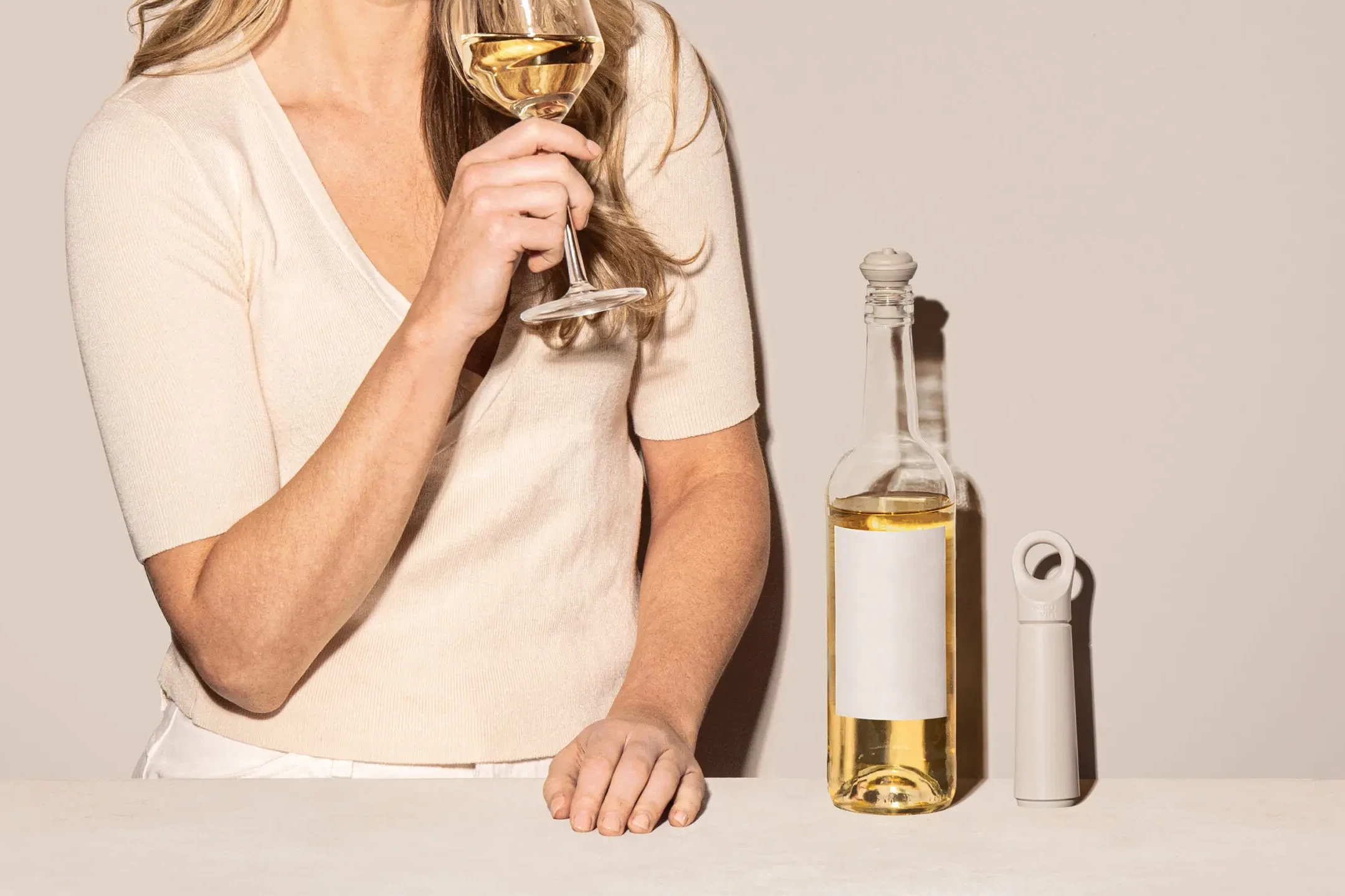
Loop Winesaver
Vacu Vin